Your Quote
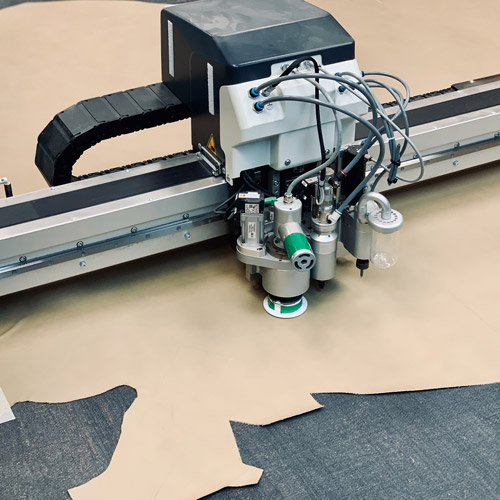
We’ve embraced modern technology within a traditional industry to enable us to deliver exceptional interior trim kits.
Our position in the industry has seen an increased demand for our products. Through digitisation, we have been able to increase capacity in our workshop and bring a consistency to our production line that could never have been achieved by hand. Whether it’s a door panel or a carpet kit, a glove box or a seat cover, our machines cut our parts with millimetre accuracy every time.
CNC Router
For flawless precision across our panelling items, we cut all our backing materials – hardboard, millboard & black grain board – on our dedicated CNC machine. We pre-cut all relevant fixing holes for attaching the panels to the car in addition to “pilot” holes for other elements required such as door handles, window winders, and fixing brackets for associated panels or parts.
Our digital patterns are taken from the same templates on which the company was founded and we have worked to improve them over the years to ensure the best quality of fit across cars that originated from an inconsistent factory production line. Our CNC cuts the most versatile versions of our panel work.
Digital Cutter
Our leathers, vinyls, carpets and all other soft materials are cut on our innovative digital cutter. With this machine, we can cut with speed and millimetre accuracy, eliminating the mistakes and discrepancies that can result from cutting these materials by hand whilst at the same time reducing waste. Our digital cutter can precisely position notches along sewn edges, providing our Sewing Department with accurate pieces from which to work and ensuring that parts are assembled correctly and consistently each time.
We invested heavily in this machinery, particularly the leather cutting technology which auto-maps pattern pieces onto the hide of leather generate the best and most efficient use of the hide according to the quality of leather required for each pattern piece. The speed, accuracy and efficiency of this machine is simply incredible. Our team used to dedicate hours of time to lay-planning patterns, particularly on leather hides as each one is unique in its shape and useable area according to scarring and blemishes. Somewhat of a headache? Absolutely. But with our digital cutter now on-site, our machinists and trimmers can happily relinquish this laboursome task and free up their time in the workshop for what they’re best at – sewing and trimming.
Once the material has been cut on the machine, we then use a projector to cast pattern information onto the cut areas so that the patterns can be loaded off the machine and organised throughout the workshop according to the processes they subsequently require, whether that’s HF Welding, Leather Skiving, Sewing or Trimming.
As we have embraced more and more technology over the years, our production line has benefited from efficiencies and capabilities unimaginable in the cottage-industry beginnings of our company, let alone in the hand-built era from which these cars originated.
And who’s to say we stop here? In our ever-evolving inter-connected digital world, we’re always looking at how technology can enhance our business. But classic cars will forever be our analogue counterpart; a reminder of an era without screens or coding or pings. And the best part? Their history is at the very essence of our business, and we are very grateful for that.
- Categories: Quality & Workmanship