Your Quote
We’ve been manufacturing interior trim kits for over 40 years and we fundamentally believe that it’s our approach to business and customer service that has brought us to where we are today.
For so long we’ve just quietly gone about doing things our way; we’re a small team of talented trimmers and machinists and we run a busy workshop making interior trim for a select range of Austin Healeys, Jaguars, Triumph TRs and MGAs. Simple. Our focused and passionate approach has equipped us with an unrivalled level of knowledge in interior trim restoration rarely matched by others in the industry.
We know what we do. And we certainly know how we do it. But more recently we’ve been spending a bit more time thinking about why we do it. Something has kept us rolling up our workshop door every morning for the last 40 years.
Time and again there’s one word that we keep coming back to that seems to sum up every facet of our business approach – quality. It starts at the very beginning with our raw materials and it runs deep throughout our production line. It’s something we’re always very aware of; from our manufacturing processes to our customer service. Quality isn’t just something you see, it’s something you feel and it’s embedded into the very foundations of our business through our materials, our processes and our people.
Our Materials
Production starts at the beginning with highest-standard raw materials. We have loyal relationships with our suppliers which span decades of business; we trust them and they trust us. We have often been approached by other suppliers offering cheaper alternatives, but we always turn them down as they inevitably fall short on quality and durability and we’re simply not willing to compromise our world-renowned reputation for the sake of saving a bit of money. We consciously choose to spend more on our raw materials to bring our customers the wealth of choice offered by our comprehensive Material & Colour library; curated to offer a varied yet concise range of materials in shades to satisfy all interpretations of original interior colour schemes.
Our library of colours offers the widest choice in the industry and we provide colour advice for all our customers which we complement with a free worldwide sample service. Using our knowledge of materials and their applications throughout the car according to marque and model, we developed a Primary & Secondary materials navigation method to assist our customers in their colour and material choices.
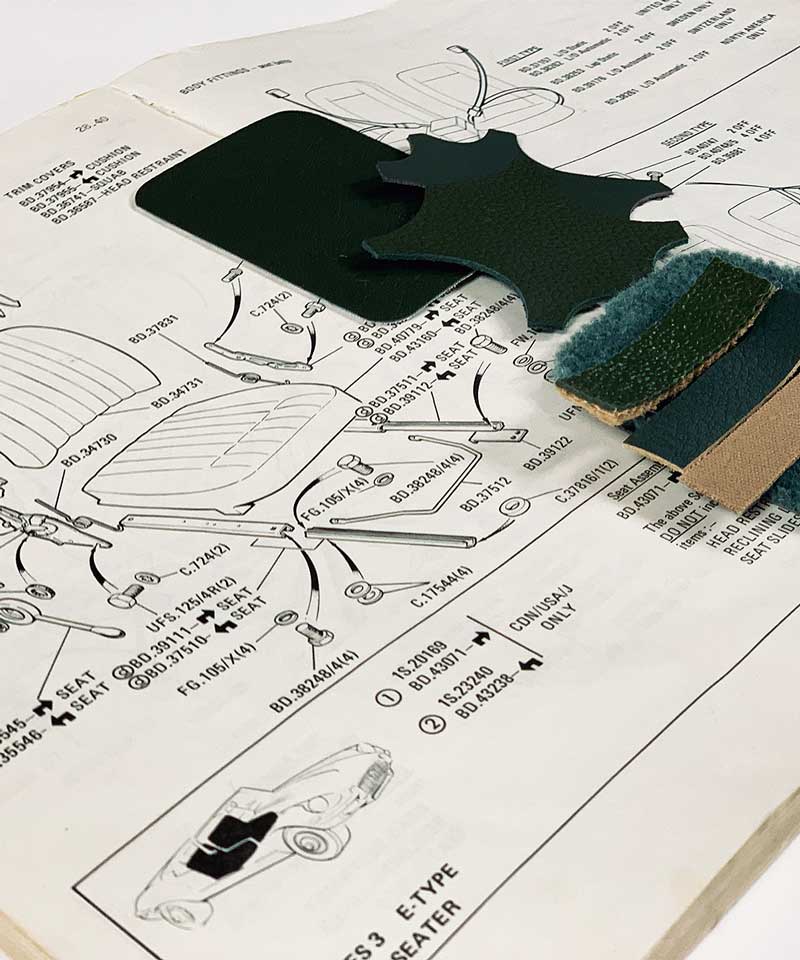
Our deep understanding of interior trim is the basis of our library; we’ve sourced all our materials based on original specification trim, but we have also engineered these where we can – such as part-glueing and pre-slitting our Leathercloth piping – to allow for a better overall finish. It’s all part of knowing our stuff – our expertise allows us to make small yet significant changes in the manufacture of our Concours quality trim without compromising originality.
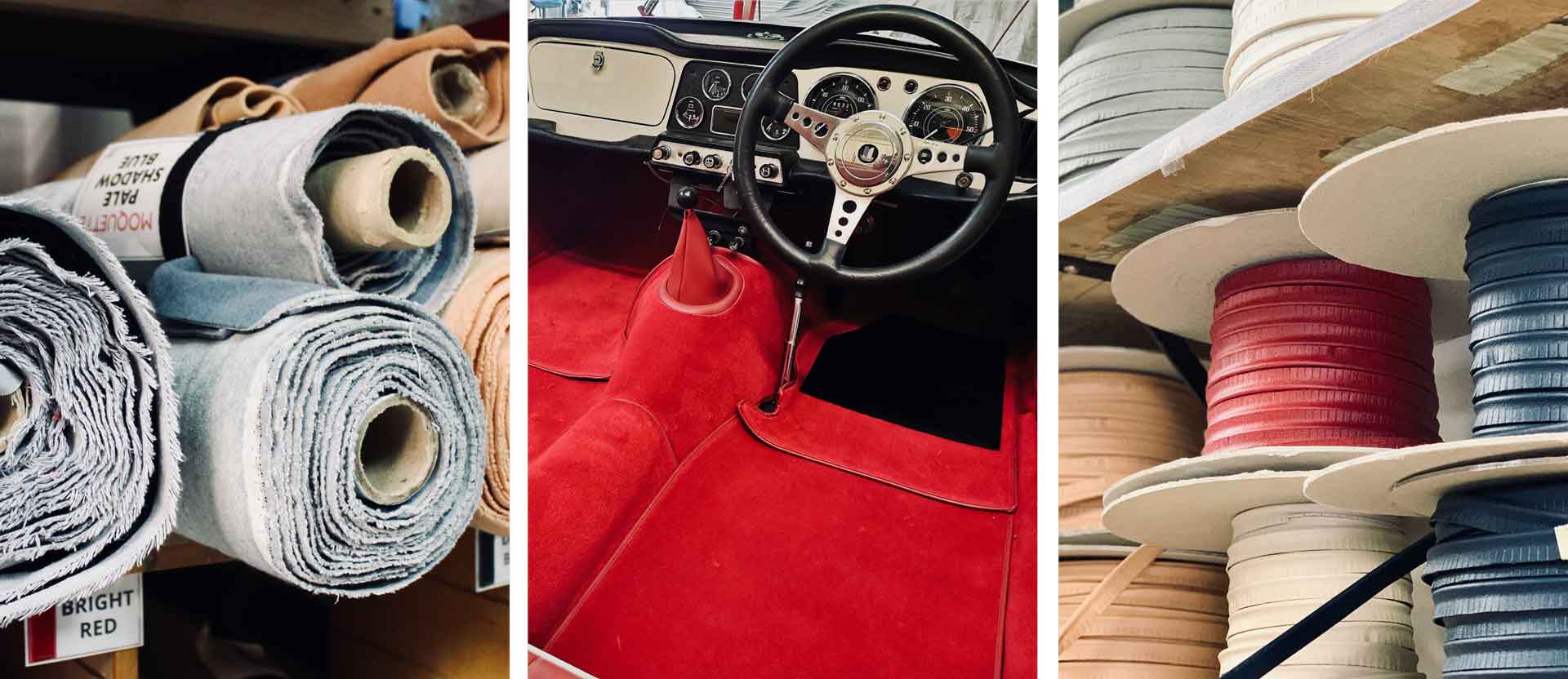
Our Processes
Over recent years we have invested heavily in our production line, replacing hand and press cutting with speedy, millimetre accurate and digitally driven CNC machinery.
And whilst these machines really give our workshop the ‘wow’ factor, it’s important to remember the patterns they’re cutting were originally made by John Skinner the best part of 40 years ago and still to this day remain the most accurate in the industry. They were made with a meticulous attention to detail – drafted only from what John knew to be original specification trim – and carry with them decades of annotations, notes and knowledge. And as John himself used to trim, he made minor adjustments to his patterns where he could see changes would be both useful and helpful. His care and attention to detail over the years means that we offer the most comprehensive kits on the market; we extend un-sewn edges of seat and headlining kits to allow for more grip when trimming; we leave loose flaps along our panel work for flexibility in fitting, and our trim kits come with extra lengths of raw material for covering over bodywork areas that were originally left exposed, but we’ve come to learn look better trimmed.
Supported by our on-site archive of original panel and seat work that we have acquired over the course of our company history, the patterns we cut and manufacture from are a world-recognised authority in original specification trim, backed by knowledge and expertise that simply can not be rivalled elsewhere.
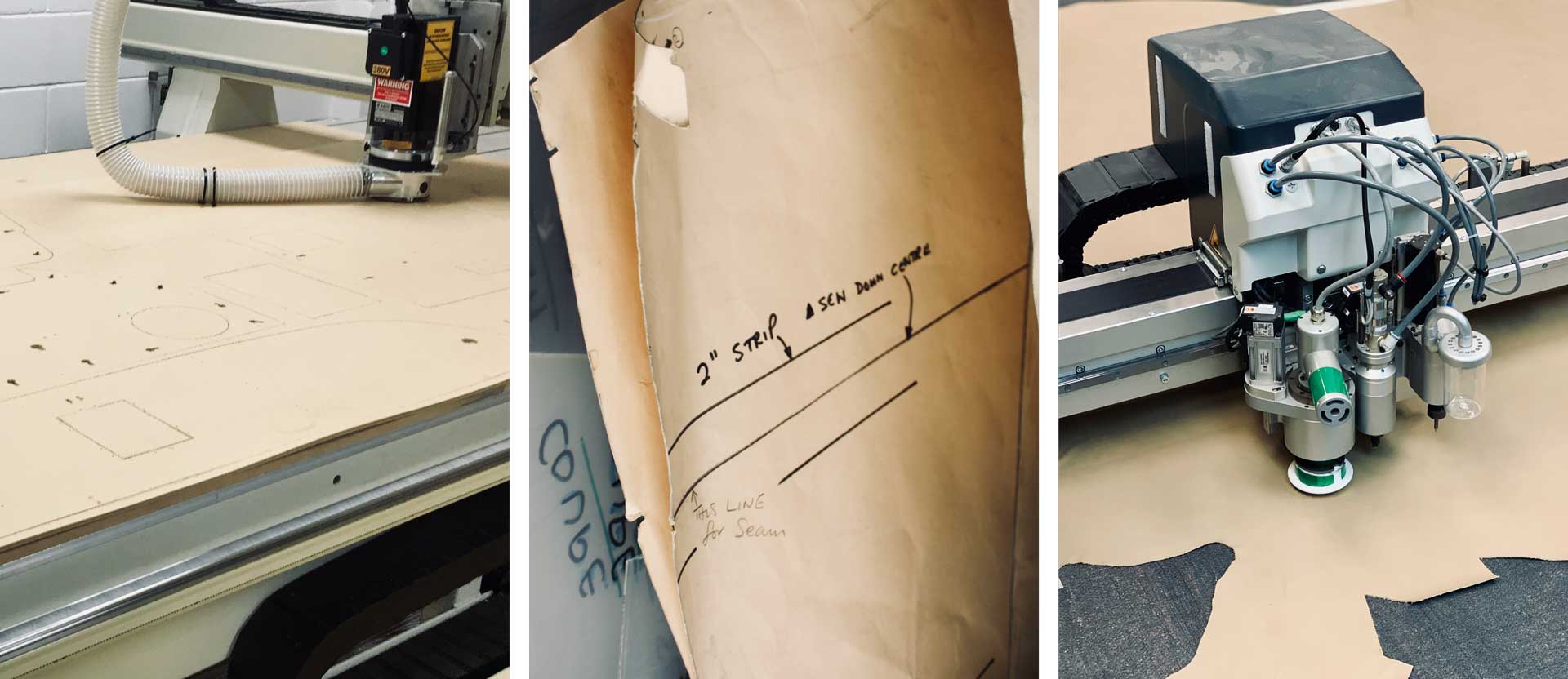
The credibility of our patterns is further strengthened by our production line processes. Our on-site High Frequency/Radio Frequency welder, alongside our weld tooling for Austin Healey Mark 3 3000 BJ8’s, Triumph TR4’s-TR6’s and Jaguar Saloon models, allows us to apply original specification weld patterns to panel and seat work – just as would have been seen on original factory production lines. John Skinner’s early investment in weld machinery and tooling – particularly for the Triumph TR’s – made him a leading figure in after-market trim from the get-go, highly regarded for the accuracy of his replica.
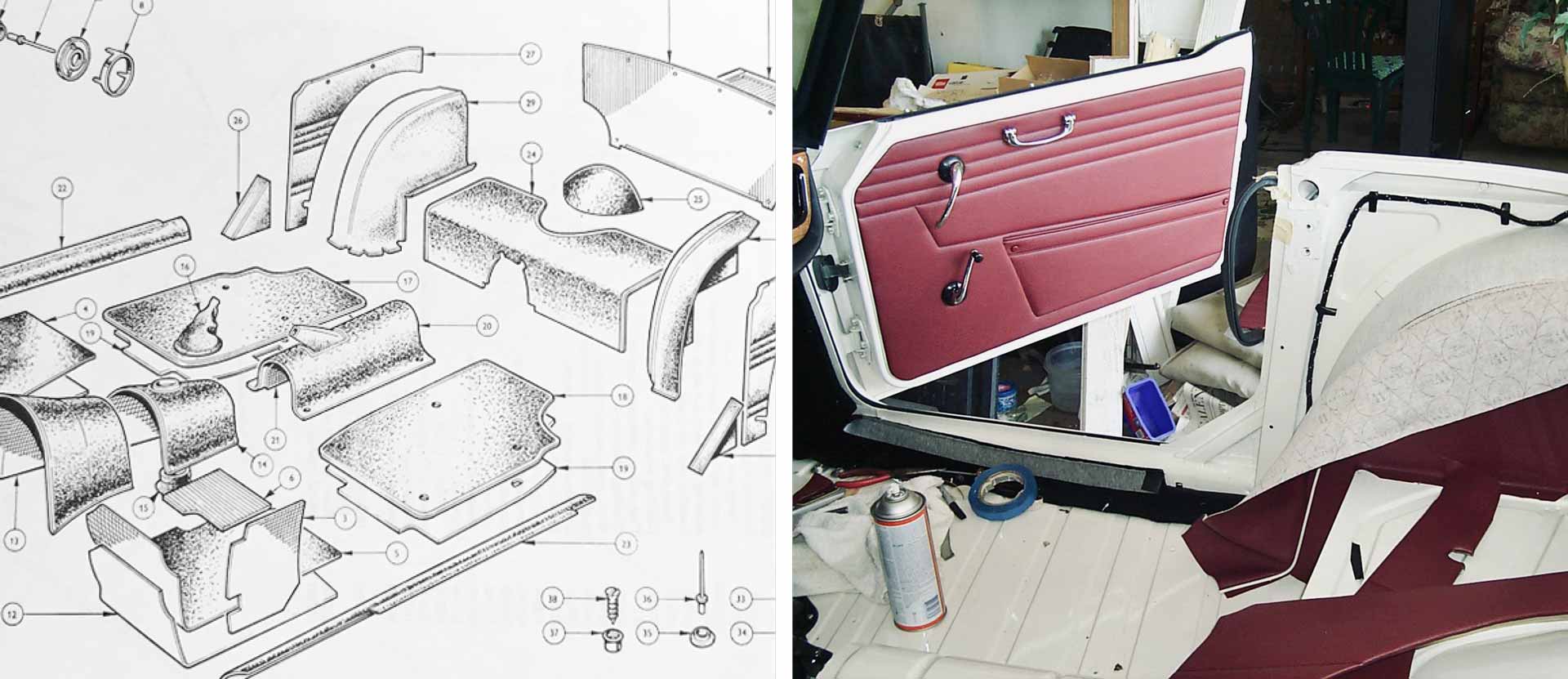
And a more recent acquisition of a Leather Skiving Machine enables us to thin down leather to a thickness more suitable for trimming intricate areas of a car interior such as ashtray brackets, centre consoles and dash facias. We could see an issue – finished interiors blemished by tucks and lumps where trimmers had done their best to work thick leather around and under corners and curves – so we wanted to help. The best part? We skive any relevant pieces within a Trim Kit as standard and at no additional cost.
Our People
Our approach to quality sinks deep into the values of our company; our team enjoy working here – we have an incredibly low employee turnover rate – and everyone takes a huge amount of pride and care in their work. We take a holistic view to our production methods, viewing the manufacture of each kit as a whole rather than breaking it up into a piece-work unit-output process. Our team are knowledgable and informed about what they do – they’re never rushed – and skilfully craft our kits with an impeccable eye for detail.
We’re a small team and always will be. We take on enough work to keep ourselves busy, but not so much that we’re overwhelmed – that’s where mistakes happen and you lose attention to detail. Our approach affords us a flexible working environment, enabling our team to fit their work around their young families, commitments and interests – we proudly boast a talented rock guitarist amongst us!
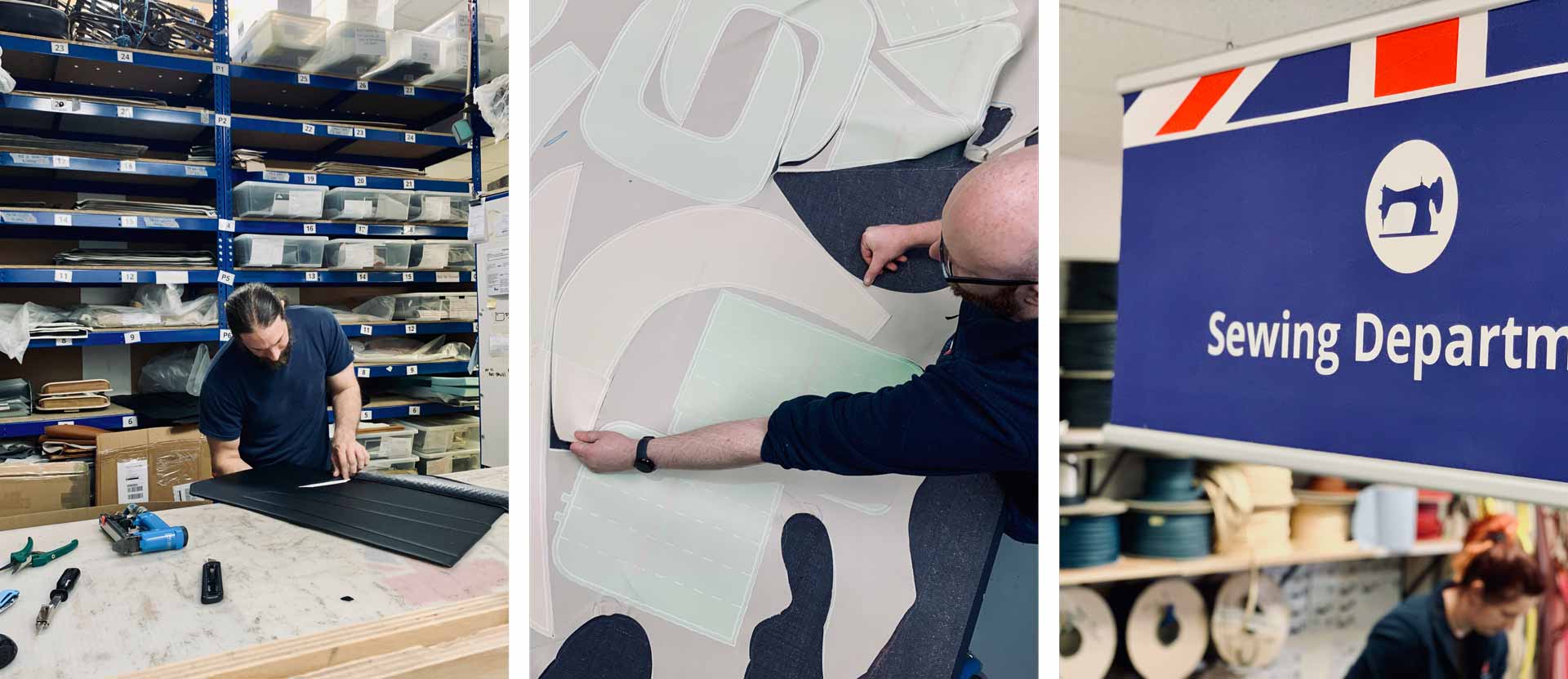
We invest in our materials, our processes and our staff because we care about our customers’ restorations, and feel somewhat of a loyalty – given the very nature of our company – to apply our expertise across all areas of our business to help keep alive the history of interior trim with a conscientious and diligent accuracy. Our approach simply can’t be matched by the mass-market, off-the-shelf manufacturers.
So where we’ve previously stayed rather quiet about what and how we do things, we feel it’s about time shouted from the rooftops…
… we know our stuff and we’re rather quite brilliant at what we do!
Our comprehensive archive of original parts alongside an extensive library of over 40,000 (and counting) reference photographs from individual parts to fully trimmed cars, makes us a leading resource in British classic car trim.
Our knowledge and records are so well respected that in recent years we have assisted Jaguar Landrover and their associated “Classic Works” division with various restorations and information for their own archives and presentation – truly a case of “the student becomes the master” – and one that we are very proud of.
The day to day workmanship values of our company, partnered with traditional British craftsmanship, attention to detail and the completeness of our interior kits makes us the choice with classic Austin Healey, Jaguar, MGA and Triumph owners, restorers and enthusiasts worldwide.
Quality, originality and value for money. And, of course, an interior that’s as beautiful as the car.
That’s our philosophy.